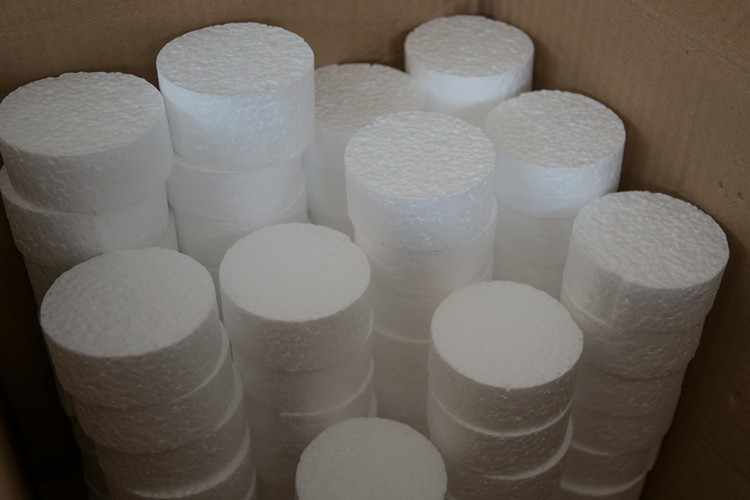
Styrofoam plugs, also known as styrofoam insulation plugs, are circular fillers designed for holes created during the installation of styrofoam insulation boards. These holes are remnants of the fasteners used to secure the insulation panels. These plugs are also occasionally referred to as dowels or discs.
Purpose of Styrofoam Plugs
Styrofoam plugs play a crucial role in improving the thermal performance and aesthetics of a building. They effectively eliminate thermal bridges and create a continuous thermal insulation layer on the facade. This helps prevent heat loss and contributes positively to the building’s overall appearance. They achieve this by mitigating the risk of condensation forming in the holes left by the fasteners, which can lead to discoloration over time. Styrofoam plugs also safeguard the fastening pins connecting the thermal insulation boards.
A styrofoam plugs, cut from a styrofoam block, ensures the thermal insulation’s integrity and maintains adequate vapor permeability. They are durable, fire-resistant, and possesses good acoustic properties. Additionally, it prevents the negative consequences of improper fastener placement, including:
- When a fastener’s flange is installed too shallow, it does not align with the styrofoam, resulting in an unsightly bulge. This requires a significant amount of adhesive for the reinforcing layer to level the walls.
- An inadequately trimmed fastening pin makes it difficult to apply thin-layer plaster, causing the plaster to crack around the protruding pin, resulting in an uneven facade.
- If a fastener is driven too deep, it creates a depression that often fills with adhesive for embedding the mesh, leading to water accumulation and the “ladybug effect.” Dark stains appear on the external insulation layer, especially on rainy and freezing days.
Styrofoam plugs effectively address the consequences of improper fastening, ensuring that the insulation performs its function without any moisture-related issues.
Is Using Styrofoam Plugs Worth It?
Styrofoam insulation plugs significantly enhance a building’s thermal properties. They create a continuous and effective insulation layer on the exterior facade, improving the building’s structural integrity and reducing heating costs. Additional benefits of this solution include:
- Time savings: installing the facade using plugs is faster and more efficient.
- Smoother surfaces: fastening irregularities such as depressions and protrusions are eliminated.
- No water condensation on the walls.
- Improved fire resistance without overloading the building structure.
- A uniform and durable exterior cladding.
How to Create Styrofoam Plugs
Insulation plugs for fasteners are manufactured from either white or graphite EPS foam. Graphite styrofoam plugs offer superior thermal properties with a very low thermal conductivity coefficient (λ ranging from 0.031 to 0.033 W/(m·K)), making them suitable for passive and energy-efficient homes. White styrofoam plugs have a λ value between 0.034 and 0.045 W/(m·K) but are less moisture-absorbent.
To create custom-sized insulation plugs, you can utilize a CNC cutting machine like the LYNX TERMCUT U130. This precise and user-friendly CNC cutter is equipped with intuitive software that simplifies the entire process, from preparing vector graphic designs to data conversion and machine control.
Cutting and Installing Styrofoam Plugs
Begin by designing the plug’s shape in the device software or importing pre-made vector graphics. Save your design for future use if needed. Arrange the plug shapes on the material to optimize material usage, then convert and automatically send the data. Ensure the cutting wire is installed, place the material on the machine’s base, and set it ready for cutting. The LYNX TERMCUT U130 provides a convenient drop-down list of cutting parameters in the software. Once settings are configured, initiate the cutting process and remove the cut pieces when done. When switching to a new design, adjustments are only needed for the material; the cutter’s settings remain the same.
To install the plugs on the fastening pins embedded in the styrofoam, create holes in the insulation boards approximately 2 cm deep where the fastening pins will be installed. Then drill holes for the pins and thoroughly clean them of debris. After inserting and hammering the pins in place, fill the gap between the insulation board and the fastener’s cap with adhesive or low-expansion foam, finishing with the styrofoam plug to conceal the hole.
Cutting styrofoam plugs with CNC hot wire cutter is an effortless process. If you are seeking a CNC machine for your business needs, explore our offerings and reach out to us to tailor a plotter to your specific requirements. We provide not only software and accessories but also essential training for your CNC equipment.