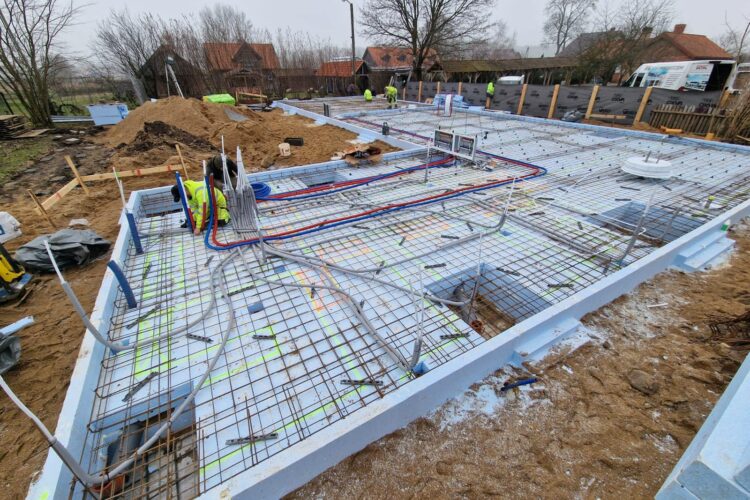
Warm foundations are a contemporary construction technology that employs styrofoam stay-in-place formwork. This innovative approach reduces construction time, lowers costs, and provides additional thermal insulation to building foundations. Lost formwork, in this context, refers to lightweight styrofoam blocks that help minimize heat loss and eliminate thermal bridges.
What is Styrofoam Stay-in-Place Formwork?
Traditional formwork typically consists of wooden boards used as molds for concrete. However, in the case of warm foundations, these boards are replaced with precisely cut styrofoam blocks. These rectangular blocks, with lengths ranging from 1 to 2 meters, are lightweight, weighing no more than 2 kilograms each. Expanded polystyrene (EPS) is the primary material used for their production. Unlike traditional formwork, where the form is removed after the concrete has set, stay-in-place formwork, as the name suggests, remains a permanent part of the foundation structure, increasing its thermal insulation properties.
Despite the lightweight nature of styrofoam, the construction can bear significant loads and withstand adverse weather conditions. Styrofoam’s insulating properties prevent moisture infiltration, mold growth, and fungal infestations. Warm foundations are increasingly being adopted in both single-family and multi-family residential buildings, gradually replacing traditional strip foundations.
Styrofoam Stay-in-Place Formwork vs. Traditional Formwork
Compared to conventional formwork, styrofoam formwork is quicker and easier to handle. It involves using ready-made products, eliminating the need to construct wooden formwork and later remove it. This streamlined approach reduces the time required for foundation pouring. Additionally, since the used styrofoam remains part of the poured foundation, waste disposal is minimized. This not only contributes to environmental sustainability but also reduces the costs associated with waste management and disposal.
Advantages of Warm Foundations
The primary advantage of warm foundations is the time and cost savings compared to traditional formwork. The laid styrofoam formwork simply needs to be reinforced with steel bars and then filled with concrete. The process is straightforward, and constructing a house using warm foundations can be up to 15% cheaper compared to standard techniques. This translates to savings in labor costs, reduced expenses for underpinning the slab, and lower rental fees for additional equipment or labor crews.
From an investor’s perspective, warm foundations also lead to reduced building maintenance costs. Styrofoam, widely used in thermal insulation, shields against external temperature fluctuations, eliminating the risk of water penetration and moisture damage. Securing foundations during the pouring phase is an effective way to maintain optimal thermal performance.
Production of Styrofoam Lost Formwork
To efficiently produce styrofoam lost formwork, you can effectively utilize a CNC machine that employs hot wire cutting technology, such as the LYNX TERMCUT U. This CNC cutter features a two-frame aluminum structure and user-friendly software that combines the features of four independent applications. With this tool, you can create vector graphic designs, convert and transmit data, set parameters, automatically arrange elements, and control the machine seamlessly.
Begin by preparing your project in the plotter software or import it from an external database. Save your project for future reference or use in other projects. Arrange the formwork elements on the material to optimize material utilization and then send the data. Ensure you properly installled the cutting wire, place the material in the cutting position, and initiate the cutting process. The LYNX TERMCUT U130 software simplifies parameter selection with a dropdown list. Configure the settings and begin the cutting process and retrieve the cut pieces upon completion. When switching to a new formwork design, adjustments are only necessary for the material; the plotter’s settings remain the same.
Creating warm foundations using styrofoam stay-in-place formwork is straightforward. After leveling and compacting the subgrade, place the formwork at the edges of the foundation wall and reinforce it with screws or mounting foam. Next, install the steel reinforcement and proceed with the concrete pouring, compaction, and leveling as you would with any other foundation. After the concrete has cured, remove the stabilizing rods and eliminate thermal bridges by filling the voids with polyurethane foam.
Want to prepare structural elements from styrofoam or or other materials amenable to cutting quickly and conveniently? Learn more about LYNX TERMCUT machines, and get in touch with our experts to see how CNC technology can simplify your work.